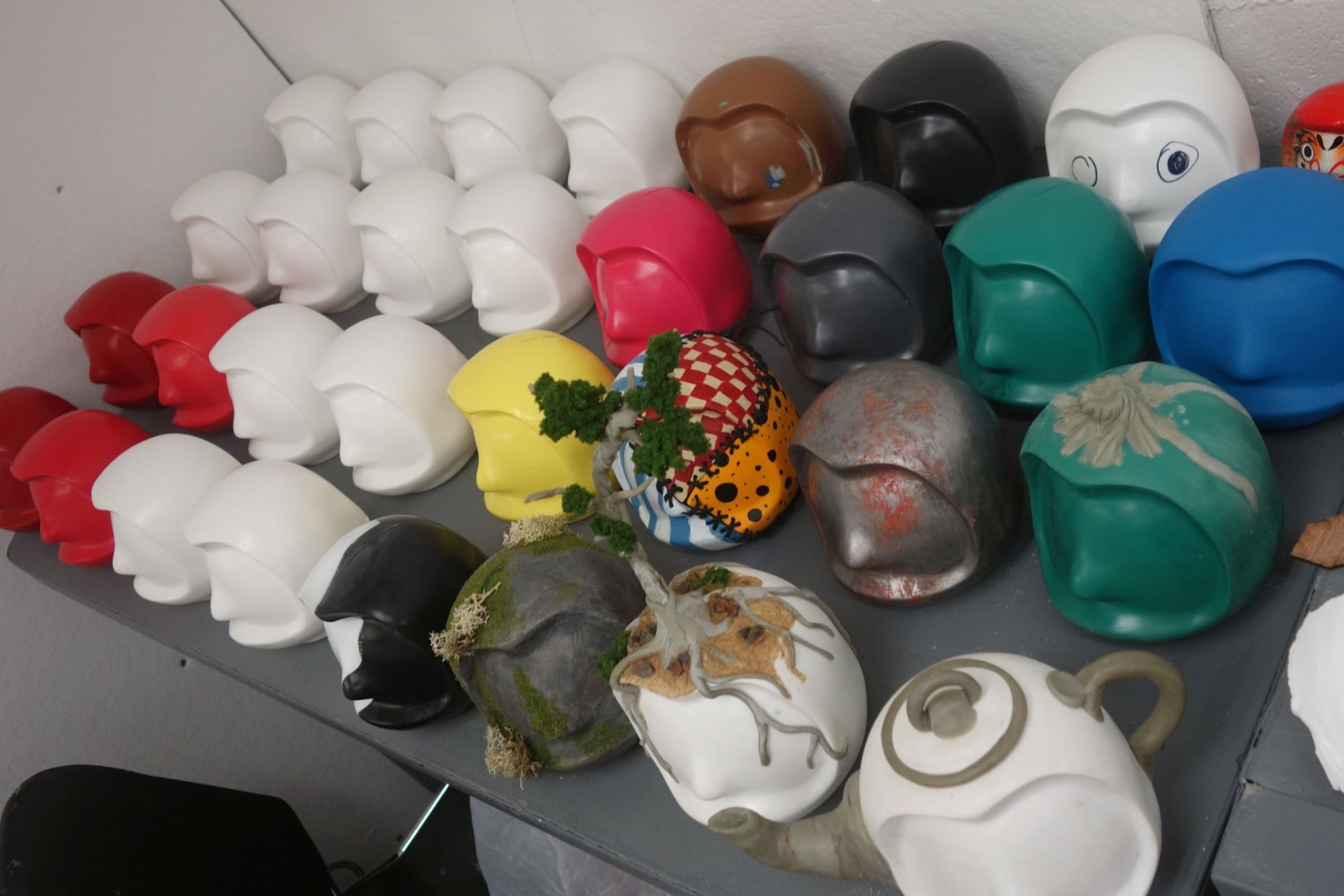
Undergraduate Senior Thesis - Daruma Project
April 2017
The Japanese daruma doll is an icon steeped in history. The doll is typically realized as a papier-mâché egg painted to resemble the Bodhidharma, a bearded monk dressed in red with no limbs or pupils in the eyes. Upon acquiring the doll, a person will decide on a goal or a wish that they desire and full in one eye; the doll will then serve as a reminder of that goal until the other eye is filled in. Though most view the object as a toy or a good luck charm, the power of an embodied promise really struck with me when I was given one of these dolls. By referencing the shape of the Daruma doll in this project I had hoped to evoke the wide variety of small and large promises, goals, and obligations that we make to ourselves and to others.
The process of creating the various iterations involved 3D printing, mold making and casting, and a broad swath of sculptural techniques.
Initial design for this project consisted of on-paper drawings both trying to understand what elements make the Daruma recognizable and what my experiences and skills brought to this concept. As an early foray into 3D modeling and design I produced a number of rough polygonal models based on the dimensions of an existing Daruma doll. This model was used to plan how I would configure the final installation, including determining the scale of my figures.
Following the digital prototyping steps I needed to bring the project back into the physical world, I took the 3D model produced in blender and used 123D Make to slice the model into many layers which could be laser cut into cardboard and reassembled. This would give me an idea of scale. One model was then covered in plaster to better approximate some of the final features. At this time I was also experimenting with other silhouettes in Adobe Illustrator. I suspected that these might be a more satisfying or recognizable shape then the original paper-mache doll. These shapes were laser cut in flat plastic so they could be compared to the other models.
After further refinement a digital 3D model was finished, and would need to be printed in plastic. With a relatively generic blank I began to think of and illustrate what might be possible to produce and in what ways they might illustrate the passage of time or the difficulty in achieving a goal that we set for ourselves. I decided to forgo the traditional eye-filling motif and instead focus on the shape of the Daruma to evoke the idea of promise making and breaking.
The finished 3D model was taken to CMU's IDeATe Labs where it was printed in PLA plastic on a NVBot 3D printer. I printed two sizes, 5.5" diameter and an 8" diameter. One of the great assets of having a 3D model is the ability to arbitrary scale the sculpture.
After the printing was finished I brought the Daruma's back to the studio and proceeded to do some re-sculpting with 'Apoxie Sculpt' modeling putty. They were also sanded and painted until the model was glossy and smooth.
Before adding silicone the master model was attached to a base and a sprue that would become an opening for casting materials to be poured inside the mold. A removable base with registration marks was also added to ensure a smooth bottoms to the model.
A soft silicone was brushed on to create a perfect negative replica of the master model. The silicone does not adhere to the master model nor will it bond with the polyurethane resin make makes up each casting. In addition once the silicone dries it creates a flexible ‘jacket’ mold allowing for easier removal of new casts.
Finally discs of silicone were added to the jacket mold to create registration points so that a rigid mother mold can be constructed around the soft silicone mold.
The final step in mold construction is making a rigid master mold around the silicone mold ‘jacket’. Silicone does a great job of preserving small details and its soft and flexible properties makes removing new castings exceedingly easy, but the thin inner layer wont hold it’s shape without external support. A rigid 'master mold' was constructed out of fiberglass ‘mat’, woven fiberglass cloth and a polyester resin. Thanks to my time creating buggies for Carnegie Mellon University's "Sweepstakes" Race I had some experience working with composite layup. This was my first fiberglass mold, it was functional but I have since improved my methodology and workflow.
With the master mold around the silicone jacket the parts are finally ready to be cast!
The project continued by building upon the cast ‘blanks’ and developing each of them into unique pieces that were variations on the themes of times passing and what that does to the goals and promises we make to ourselves and one another, to they rust and tarnish, do they bloom and grow, are they re-evaluated and assembled out of many pieces, do they shatter or are they forgotten.
The final showing was presented at Carnegie Mellon’s Miller Gallery on May 5, 2017.